The BTD-8X combines Controlled Automation's shape cutting and high speed drilling technologies to produce top quality thermally cut contoured parts with drilled and/or thermally cut holes. With a core machine design of strength and stability, fast and responsive controls, and the advantages of high definition plasma and high speed carbide drilling, accurate high quality parts are created quickly and easily with the BTD-8X.
The drill tool feeding system uses a precise closed loop AC servo ball screw assembly. Velocity, torque, and position are all controlled at a 1 KHz sample rate. Through spindle coolant is also used at the front of the cutting edge of the drill bit for a minimal use of coolant and less mess.
- Laser-Measuring of the plate for higher speeds and accuracy
- High-Speed Carbide drilling
- High Speed Rapid Traverse System
- Water or down-draft cutting surfaces
- Tool carriage and gantry is guided by Precision guide rails
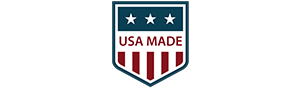
USA πΊπΈ manufactured
From the design to the steel itself, we produce USA manufactured solutions.
Service
Our in-house service technicians offer minimal downtime and free phone support for the life of your machine.
Local Parts
We offer customers with off-the-shelf and readily available parts for the best uptime possilbe and less costs.
Windows control
The Windows control allows for simple service and operation in a familiar and easy to work in environment.
Machine Specifications | |
Spindle | #4 Morse Taper / 10HP |
Maximum Spindle Speed | 1,200 RPM Variable |
Drilling Capacity | Up to 2-1/2" thickness |
Drilling Capabilities | 1-9/16" max diameter (40mm)
No tool-changer Automatic Pilot-Hole drilling for torch/plasma edge start |
Coolant System | Thru-Spindle Coolant |
Maximum Width | Up to 8β (2.44m) |
Maximum Travel Length | Up to 153β (46m) |
Maximum material thickness | 6β piercing start with Oxy-fuel (152mm) |
Cutting Surface | Various Configurations of Down-Draft or Water-Table (preferred) |
Both the motion of the gantry and length axis is driven along a linear rail and block system by use of AC Servo motors (one on each side of the gantry for movement in the X axis and one for tool movement in Y) coupled to low backlash planetary gear reducers. We use the highest quality gear reducers on the market to reduce backlash when changing directions and to ensure a very long dependable lifespan. The planetary system produces extreme power and performance in a very small package. Helical rack and pinions are used to reduce cogging and vibrations that are typical when using straight rack and pinions. When combined in a system, AC servo motors and helical rack and pinion provide smooth motion and high acceleration rates, producing optimum plasma and oxy-fuel accuracy and cut quality.