The isoMAX uses Controlled Automation’s shape cutting technology to produce top quality thermally cut parts. The isoMAX offers contour bevel-cut parts with either the HPR Orbital Bevel™ system or the XPR BevelMAX. With a core machine design of strength and stability, fast and responsive controls, along with the advantage of oxy-fuel and high definition contour plasma cutting, precision parts are created quickly and easily. The isoMAX has many options to fit your specific needs. You can outfit your machine with up to 4 oxy- fuel torches, and 1 contour plasma. This machine can be customized to fit your exact requirements, with multiple tool stations, customized operator controller positions, features such as variable travel lengths, widths, service track positions and material handling
The machine bridge is a tubular steel section with a 1” thick main face that has been stress relieved after welding, then machined down its length to provide a flat, straight seat for the guide rails. This provides superior accuracy for all tool motors. The bridge is driven along the rail system length by use of dual AC servo motors (one on each side) coupled to low backlash planetary gear reducers. Helical rack and pinions are used to reduce cogging and vibration as normally witnessed when using straight rack and pinions. When combined in a system, AC servo motors and helical rack and pinion provide smooth motion and high acceleration rates, producing optimum plasma and oxy-fuel cut quality and accuracy
- Laser-Measuring of the plate for higher speeds and accuracy
- Contour Bevel capable
- Oxy-fuel cutting, high-definition plasma, ink-jet marking and more
- Large capacities of up to 23ft wide and 153ft long
- Various options for water-table and down-draft cutting surfaces
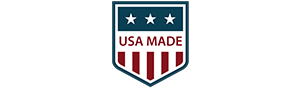
USA 🇺🇸 manufactured
From the design to the steel itself, we produce USA manufactured solutions.
Service
Our in-house service technicians offer minimal downtime and free phone support for the life of your machine.
Local Parts
We offer customers with off-the-shelf and readily available parts for the best uptime possilbe and less costs.
Windows control
The Windows control allows for simple service and operation in a familiar and easy to work in environment.
Machine Specifications | |
Approximate fully loaded gantry weight | 8,000 lbs (3,632kg) |
Maximum travel speed | 750”/min (19m/min) |
Material width capacity | 6’ to 23’ (1.8m to 7m) |
Maximum travel length | 153’ (46m) |
Maximum material thickness | 6” piercing start (152mm) |
Cutting Surface | Various Configurations of Down-Draft or Water-Table |
The bridge is driven along the rail system length by use of dual AC Servo motors (one on each side) coupled to low backlash planetary gear reducers. We use the highest quality gear reducers on the market to reduce backlash when changing directions and to ensure a very long dependable lifespan. The planetary system produces extreme power and performance in a very small package. Helical rack and pinions are used to reduce cogging and vibrations that are typical when using straight rack and pinions. When combined in a system, AC servo motors and helical rack and pinion provide smooth motion and high acceleration rates, producing optimum plasma and oxy-fuel accuracy and cut quality.
The bridge is supported by four pivoting wheel assemblies. Each pivoting wheel assembly houses two hardened support wheels for a total of eight wheel supports. By supporting the gantry with eight wheels in contact with the rail surface instead of four, the lives of the wheels, support rail, and wheel bearings are doubled. The wheel assemblies on the guide side are “V” groove wheels which guide the machine on the same path as the guide side rail rolling surface. The wheel assemblies on the opposite side of the gantry are flat across the wheel face. This allows for thermal expansion and compliance between the machine and the rail system interface. The rail rolling surfaces are hardened and ground round shafting running the length of each rail. This provides a very durable long lasting support for the bridge. Another advantage of the IsoMAX rail system is that the round shafting allows debris to fall away from the rolling surface naturally without the use of mechanized cleaning devices that fail over time.